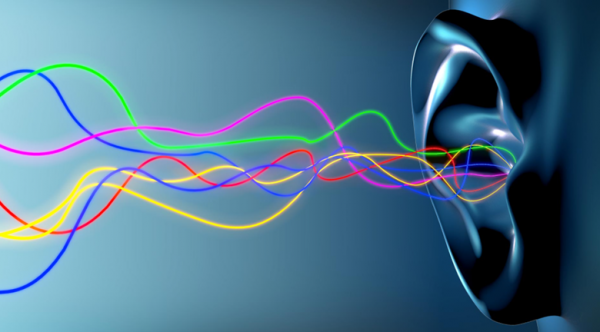
Airborne Noise
The primary strategies for reducing airborne noise are absorbers and barriers. Lightweight open cell foams are a very cost-effective way of attenuating noise in the air; particularly low frequencies. The open cell structure can absorb sound waves reducing the amplitude of the wave as the sound energy is transformed into heat. These materials include open cell polyether and polyester foams as well as reticulated (cell walls are removed to increase porosity) foams.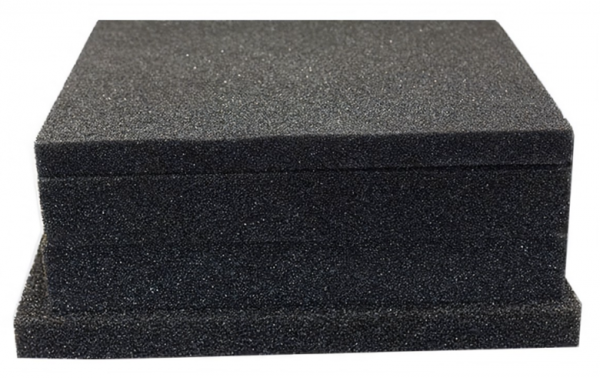
(Open Cell Urethane Foam)
Low density, closed cell foams can act as both an absorber and a blocker and do better with medium to high frequencies. PVC and low density cross-linked polyolefin foams can be used in these applications. Synthetic blanket materials such as 3M Thinsulate and fiberglass composite materials are also effective solutions for attenuating unwanted airborne noise. These materials can be supplied with a pressure-sensitive adhesive backing to facilitate easy installation and are easy to die cut into the final shape using flat bed, waterjet or flash knife cutters. Low density, closed cell foams can act as both an absorber and a blocker and do better with medium to high frequencies. PVC and low density cross-linked polyolefin foams can be used in these applications. Synthetic blanket materials such as 3M Thinsulate and fiberglass composite materials are also effective solutions for attenuating unwanted airborne noise. These materials can be supplied with a pressure-sensitive adhesive backing to facilitate easy installation and are easy to die cut into the final shape using flat bed, waterjet or flash knife cutters.Structural Noise
The solutions for structural noise are a bit different. In a manufacturing environment, machinery is the typical source of vibrational noise. In a car, the engine and associated systems are usually the sources. Left unchecked, the repetitive motion of parts and surfaces can result in material fatigue and reduce reliability over time. Isolation is one of the principal strategies to minimize vibrational noise. Dense foams and microcellular foams are ideal material choices for use with heavier objects as these foams decouple the source from surrounding surfaces or housings that would otherwise amplify the sound and vibrations. These materials can be offered with or without adhesive and are easy to die cut for easy application. In some applications, bonding and isolation can be accomplished in one step. The use of acrylic foam tapes such as 3M VHB permit two rigid surfaces to be bonded together (for example a metal building façade panel to a stiffener). Any vibrational energy places the tape into elongation mode even though it is constrained by the two rigid surfaces. (constrained layer damping) The energy is transformed into heat as it damps the vibrations. Another strategy to use constrained layer damping is to apply a thick foil with a soft pressure sensitive damping adhesive such as 3M’s Vibration Damping Foil Tape. The thick foil acts as a constraining layer and the adhesive goes into elongation mode converting the vibrations into heat. Again, these products are easy to die cut and apply. Tom Brown, Inc has the experience to help you address your noise and vibration challenges with a broad portfolio of foams and tape products designed to meet your needs. Contact us today at www.tbi.com. There are truly some fantastic buildings that were recently built or are in the construction process. The curtain wall, window wall and metal building panel designs have pushed the envelope in terms of aesthetics and environmental performance. Our eyes are immediately drawn to the glass, metal panels, and other features as they should be because the real beauty is truly there. However, I’m always curious about the things behind all that beauty; the thousands of fasteners, caulking, backer rod, tapes, and other components that help hold it all together and make it functional. I was walking by the waterjet the other day and saw windowsill splice blocks being cut for a metal building panel project. It got me thinking about many of these small, seemingly insignificant parts that we provide or façade applications. Sometimes, these small parts play a big role!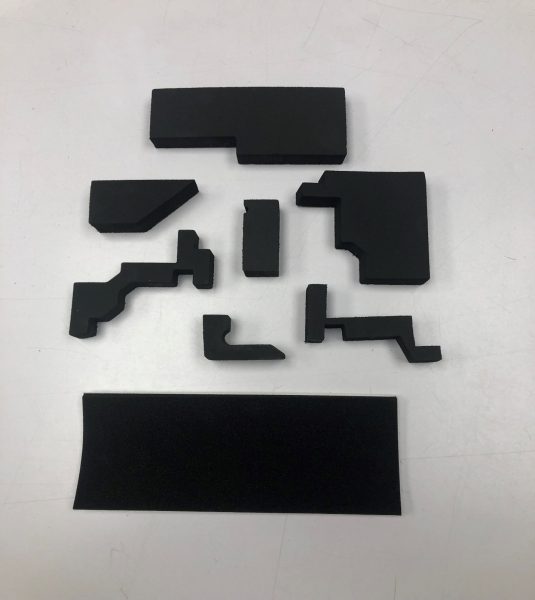
Foam Technical Properties for Façade Applications
There are a number of choices for the elastomeric foams that might be considered for these types of parts. One of the workhorse products is SCE41B from Rubberlite, Inc. SCE41B is a blended foam consisting of neoprene, EPDM and SBR (styrene butadiene rubber). This blend offers excellent oxidation and ozone resistance, resistance to acids and alkali, and passes UL 94 HBF burn tests. This foam is easy to compress for easy installation yet has high enough tensile strength for easy removal.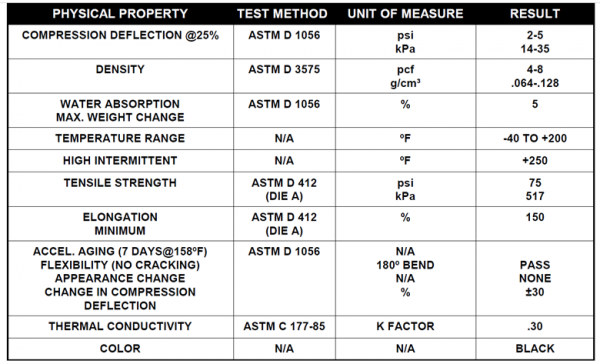
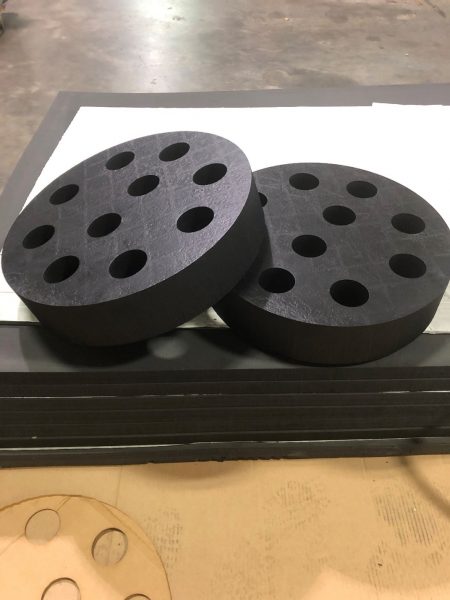
Cutting thick, soft foam materials accurately can be challenging. If you try cutting them with a knife, the foam compresses. As the foam thickness increases, blade deflection increases. Sometimes a steel blade simply isn’t the answer.
Enter the waterjet cutter. The waterjet creates a needle-like stream of water about 0.010” in diameter that is under 60,000 PSI of pressure. At that pressure, the speed of the water exiting the nozzle is almost supersonic. (which is why waterjet cutters can be a bit loud).
The Case Study
Geotechnics is a group of really smart guys in East Pittsburgh, PA who understand a lot about testing dirt. They offer extensive geotechnical and geosynthetic testing services that support the energy, highway, civil, and landfill industries.
One of their testing projects involved collecting soil samples from hundreds of feet below the surface. The sampling process involved a cylindrical steel tube that was pushed down through the soil using a ram to collect the soil specimen. The tube was capped and then brought back to the surface.
It was critical that the sample remained undisturbed through the shipping process. The tubes were 3 feet long and multiple tubes needed to be supported in a drum for transport.
Randy O’Rourke and his team from Geotechnics met with our CEO Kenny Brown about potential solutions.
Solution
The tubes were heavy and required support on the top and bottom to maintain a vertical position. Damping vibration during transport was also key to maintaining sample integrity. Kenny suggested a thick, closed cell foam that would be cut to match the diameter of the sample cylinders with support on the top and the bottom of the tubes.
A 4” thick, closed cell foam made from Armacell’s Ole Tex® BDJN 200 was selected. This foam is a blend of polyethylene and EVA (ethylene vinyl acetate). The polyethylene is chemically compatible with the EVA which adds softness and flexibility to the foam matrix.
A CAD drawing was created to produce a part to match the diameter of the drum and to support 10 sample tubes. Sample parts were cut and given to Geotechnics for testing.
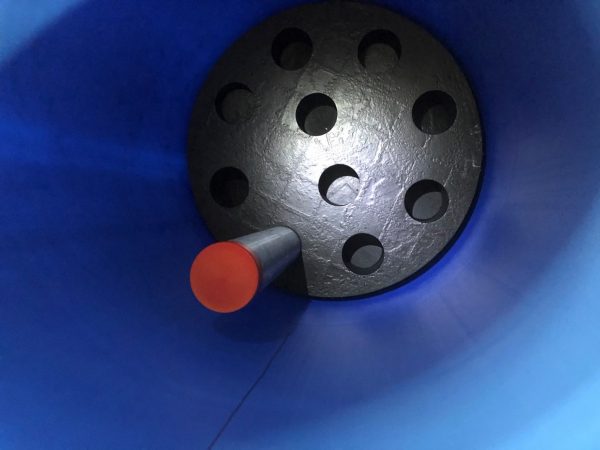
Why Waterjet?
Waterjet cutting has significant advantages when cutting large parts from thick, soft foams:
- The narrow cut width or kerf permits cutting intricate shapes with minimal deflection so there is minimal material distortion
- No heat is involved unlike a laser cutter which can melt or char the edges of the finished part
- Cuts very square, even on thick foam materials
- No tooling is required. Once the CAD program is loaded into the waterjet, it’s ready to cut.
- Easy to fabricate one off prototypes to test a design and make sure it functions properly
- No chemicals or hazardous waste from the cutting process
- Can handle part sizes up to 60”x 120”
Want to learn more about how Tom Brown, Inc. can create waterjet parts to solve your design challenges? Visit us at www.tbi.com