Why Use Foam Tapes?
It comes down to two words- consistency and reliability. Foam tapes are manufactured to precise specifications in terms of thickness, physical properties, and cut part dimensions. This means that you’re applying the same amount of product every time and that translates to consistency. By contrast, liquid adhesives have much high variability and mess associated with their application and mechanical fasteners require tools and often the bond lines exhibit point pressure where the fastener is installed. With foam tapes, stresses are uniformly distributed around the perimeter or bond line evenly. Tapes are viscoelastic and have excellent fatigue resistance. While vibration and joint flexing can compromise mechanical fasteners, tapes dampen vibration and absorb shocks allowing the joint to recover time after time.Common Types of Foam Bonding Tapes
The most common types of foam tapes are acrylics, polyurethanes, and polyethylenes.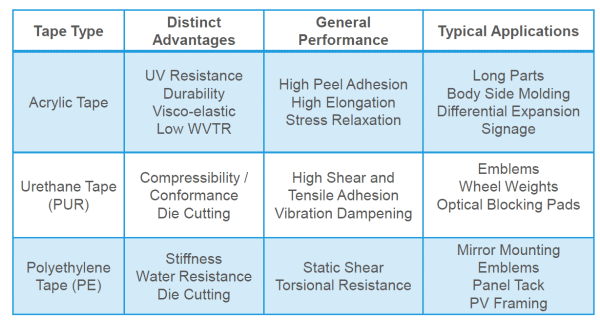