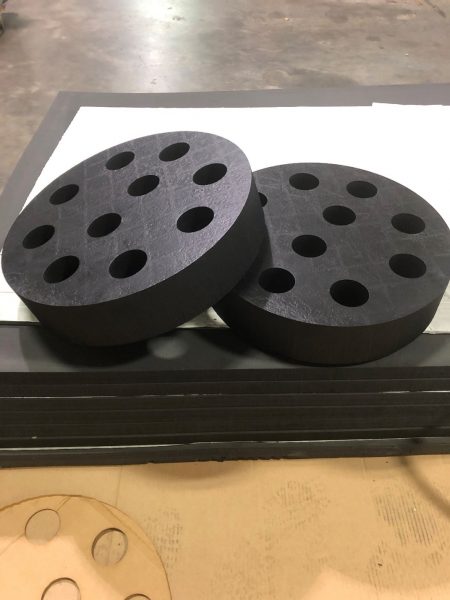
Cutting thick, soft foam materials accurately can be challenging. If you try cutting them with a knife, the foam compresses. As the foam thickness increases, blade deflection increases. Sometimes a steel blade simply isn’t the answer.
Enter the waterjet cutter. The waterjet creates a needle-like stream of water about 0.010” in diameter that is under 60,000 PSI of pressure. At that pressure, the speed of the water exiting the nozzle is almost supersonic. (which is why waterjet cutters can be a bit loud).
The Case Study
Geotechnics is a group of really smart guys in East Pittsburgh, PA who understand a lot about testing dirt. They offer extensive geotechnical and geosynthetic testing services that support the energy, highway, civil, and landfill industries.
One of their testing projects involved collecting soil samples from hundreds of feet below the surface. The sampling process involved a cylindrical steel tube that was pushed down through the soil using a ram to collect the soil specimen. The tube was capped and then brought back to the surface.
It was critical that the sample remained undisturbed through the shipping process. The tubes were 3 feet long and multiple tubes needed to be supported in a drum for transport.
Randy O’Rourke and his team from Geotechnics met with our CEO Kenny Brown about potential solutions.
Solution
The tubes were heavy and required support on the top and bottom to maintain a vertical position. Damping vibration during transport was also key to maintaining sample integrity. Kenny suggested a thick, closed cell foam that would be cut to match the diameter of the sample cylinders with support on the top and the bottom of the tubes.
A 4” thick, closed cell foam made from Armacell’s Ole Tex® BDJN 200 was selected. This foam is a blend of polyethylene and EVA (ethylene vinyl acetate). The polyethylene is chemically compatible with the EVA which adds softness and flexibility to the foam matrix.
A CAD drawing was created to produce a part to match the diameter of the drum and to support 10 sample tubes. Sample parts were cut and given to Geotechnics for testing.
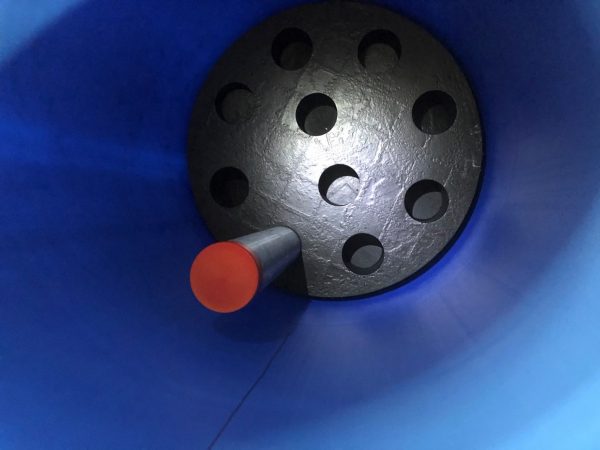
Why Waterjet?
Waterjet cutting has significant advantages when cutting large parts from thick, soft foams:
- The narrow cut width or kerf permits cutting intricate shapes with minimal deflection so there is minimal material distortion
- No heat is involved unlike a laser cutter which can melt or char the edges of the finished part
- Cuts very square, even on thick foam materials
- No tooling is required. Once the CAD program is loaded into the waterjet, it’s ready to cut.
- Easy to fabricate one off prototypes to test a design and make sure it functions properly
- No chemicals or hazardous waste from the cutting process
- Can handle part sizes up to 60”x 120”
Want to learn more about how Tom Brown, Inc. can create waterjet parts to solve your design challenges? Visit us at www.tbi.com