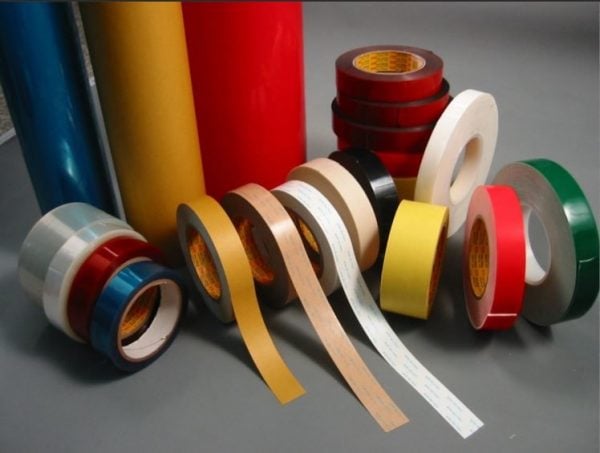
Many of us have a roll of masking or duct tape that’s been sitting in our garage or basement for quite a while. It probably doesn’t unwind as easily as it did when it was new and it might look a little rough.
What you are observing is the interplay between shelf life and storage conditions. Tapes and die cut parts made from tape products come with a shelf life and a set of recommended storage conditions. It’s easy to overlook this seemingly mundane information but it’s important to understand them both so that you get the best performance from your products.
Shelf Life
All reputable tape manufacturers list the recommended shelf life for their products. The most common time frames listed are anywhere from 6 months to 2 years. The primary reason for the difference in shelf life is the composition of the tape itself; the adhesive system, the backing, and release liner if it has one. Certain adhesive systems such as acrylics and silicones are very stable chemically and resist aging. Other adhesives such as rubber/resin systems often have antioxidant and UV stabilizer packages added to improve aging characteristics.
Another factor in determining shelf life is an aging study. Aging studies can be conducted using natural or real time aging, accelerated aging, or a combination of both. Real time aging is very reliable but is not always practical as this process can require too much time to get to market.
Accelerated aging is a procedure that utilizes elevated temperature as a way of exposing the tape or die cut part to stresses that will simulate real time aging in a compressed time frame. Physical testing on the aged tape specimens (peel, tack, shear, and liner release) are performed after exposure and this data can be compared to room temperature control samples and real time aged samples to understand which properties might have been negatively affected by the accelerated aging conditions. The stability of the physical properties can then be used as evidence to establish a shelf life.
The last factor is determining shelf life is risk management. Risk management is where product managers, business leaders, and legal tend to get involved. They typically consult with the technical group to get a recommendation but they will decide how much risk they are willing to incur as a business and this will influence the stated shelf life. Some companies are more risk averse than others and their shelf life statements often reflect this bias.
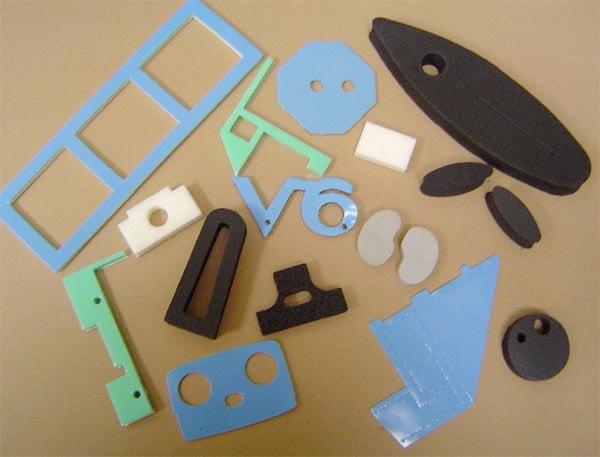
Storage Conditions
There tends to be strong agreement among tape manufacturers that optimum storage conditions are 70°F (21°C), 50% relative humidity, out of direct sunlight.
Some will expand this by quoting a range; 70°F +/- 20°F and 50% RH +/- 20% as an example. There is little doubt that optimum storage conditions will maximize (and even prolong in many cases) shelf life.
Tapes and die cut parts are stored in warehouses most of the time. Some of these warehouses are temperature and even humidity controlled. Many of them are not. Warehouses can experience large swings in temperature and humidity as the seasons change. If your warehouse sees large swings in temperature; particularly high temperatures over 95°F, the tape is experiencing accelerated aging in a similar way to a formal aging study.
Extending Shelf Life
We are often asked if a tape or die cut part is “still good” after it may have been at the customer’s facility for an extended time; usually beyond stated shelf life. The good news is that unlike the fairy tale “Cinderella”, tapes and die cut parts don’t turn into a pumpkin at midnight of their shelf life. The performance of most tapes is not projected to change significantly even after the shelf life expires.
In most cases, questions will be asked about storage conditions and then the tape or die cut part can be inspected to check appearance and tack and compared against unaged material. Samples can also be sent for physical testing either to the tape manufacturer or an outside lab.
If the material has not been adversely affected and especially if it has been stored correctly, the shelf life might be able to be extended for a short period of time.
Summary
The shelf life and storage conditions are often the most overlooked items on a technical data sheet. Most tape products list a 6 month to 2 year shelf life. Shelf life is determined by the composition of the tape, backing, and release liner along with aging studies that document the performance of the tape in real time and/or accelerated aging conditions.
Optimum tape and die cut part storage conditions are usually listed at 70°F (21°C) and 50% relative humidity but warehouse conditions are usually more variable than the ideal. The best way to understand how to store your tapes or die cut parts is to talk with a knowledgeable converter. Contact us at www.tbi.com