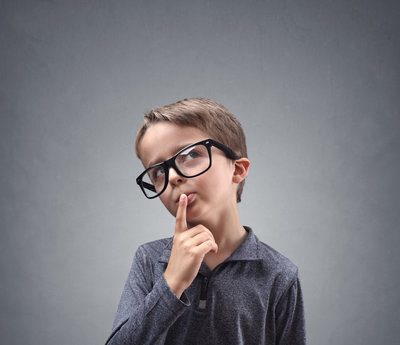
- The type of assembly being considered
- The materials to be bonded (substrates)
- The manufacturing process itself
- What the product encounter during its’ life cycle(end use requirements)
- Cost considerations
Adhesive Chemistry 101
There are three basic pressure-sensitive chemistries:- Rubber based or rubber/resin as it’s sometimes called
- Acrylics
- Silicones
Rubber Based
The oldest type of pressure-sensitive adhesive consisting of a rubber (natural or synthetic) that is tackled by the addition of various resins.Pros
- Can be easily formulated
- Adheres quickly to many surfaces
- Economical
Cons
- Poor temperature resistance
- Poor chemical resistance
- Variable UV resistance
Acrylics
The “workhorse’ of the tape world.Pros
- Tack, peel, and shear can be varied
- Good UV resistance
- Good temperature resistance
Cons
- May not adhere quickly
- More expensive than rubber
Silicones
The most “specialized” of the three.
Pros
- Balanced peel and shear
- Excellent temperature resistance
- God UV resistance
Cons
- Low tack and quick stick
- Very expensive