The Basics
A transfer adhesive is a coating of pressure-sensitive adhesive on a release liner. The majority of transfer tapes range in thickness from 1-5 mils although there are some specialty products that fall outside this range. There are also reinforced transfer adhesive versions that use fiberglass stands or thin, open scrims to help reinforce the adhesive making them more of a hybrid. By contrast, a double coated tape has a coating of pressure-sensitive adhesive coated on both sides of a carrier. This carrier is often a film (polyester, polypropylene, UPVC) but could be also be paper or tissue.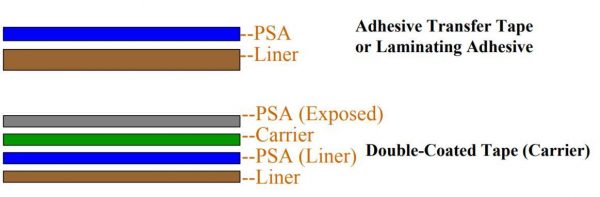
- Stabilizing the adhesive
- Allows different adhesives or thicknesses to be used on each side
- Adds thickness and dimensional stability
- Improves handling
- Can provide a barrier between the adhesive layers
Overall Comparison
Double Coated Tape / Transfer Adhesive
Typically thicker (3-10 mils) / Typically thinner (1-5 mils) Less conformable / More conformable Easier to dispense / More difficult to dispense Can be spooled / Difficult to spool unless reinforced Reinforces substrate / Does not reinforce substratePart Geometry
The shape of the part to which the tape will be applied plays a significant role in choosing a transfer adhesive or a double coated tape. When you want to bend the tape around sharp edges or compound curves, transfer adhesives have the advantage. The lack of a carrier enables the adhesive layer to more really conform and remain adhered to the surface provided the right adhesive type and thickness have been selected. A carrier can often induce forces into the bond line that cause the tape to “flag” or lift as it tries to go back to equilibrium.