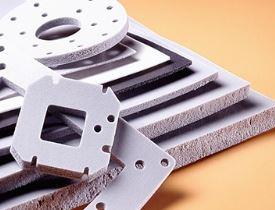
Form Factors
Silicone materials are not just “one thing” but rather an interesting portfolio of options. There are sponge rubbers, solid silicone, reinforced silicones, and foam rubber. The durometer or “hardness” can be adjusted and specified depending on whether the material is to be used for gasketing/sealing applications or for impact/vibration damping applications.Adding More Functionality
Silicone foams, sponges, and rubber substrates can be enhanced further by adding adhesive layers for easy bonding and attachment. Silicones exhibit low surface energy, which can make them a bit tricky to laminate with adhesives and achieve good adhesive anchorage. Tom Brown, Inc. has the know-how to modify the surface to permit lamination with either silicone or acrylic adhesive systems for gasket attachment or general bonding. Silicone pressure-sensitive adhesive exhibit temperature performance similar to that of the silicone elastomers (100°F to +500°F). Acrylic adhesives are a cost-effective option for some applications, but you trade away some of the temperature range. These adhesives will typically work in the -20°F to +350°F range. These options can be delivered as die cut parts by rotary, flat bed, or Waterjet die cutting techniques Typical applications include heaters, commercial lighting, oven seals, medical equipment, aerospace seals, and electronics.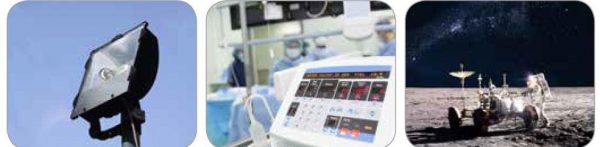