One of the first questions anyone in the tape industry asks is “What surface(s) are you trying to bond or stick to?”
This screening question provides some initial clues into how challenging it might be to adhere to the surface. It also provides insight into what tapes or adhesive systems might be best suited for the application.
Aside from questions on chemical and temperature resistance, they might also ask about surface energy, roughness or texture.
Let’s look into these questions and why those in the tape industry ask them.
Surface Energy
The standard definition of surface energy is “the excess energy at the surface of a material compared to the bulk.” This “excess energy” exists because the molecules at the surface are not surrounded on all sides by other molecules.
Surfaces that have a predominance of carbon-hydrogen bonds tend to have low surface energy (LSE) and do not wet easily. For example, you can see this with a freshly waxed car like in the photo above and also with plastics such as polyethylene and polypropylene.
Surfaces that contain oxygen-carbon bonds, nitrogen or other halogens tend to exhibit higher surface energies and better adhesion properties.
The unit used to measure surface energy (for solids) and surface tension (for liquids) is dyne/cm—or more commonly “dynes.” Metals, such as aluminum (850 dynes) and stainless steel (700-1100 dynes), exhibit high surface energies and are easy to adhere to for almost any adhesive.
Bonding starts to become a bit more challenging when you get to EVA at 33 dynes, polyethylene at 31 dynes and powder coat paints in the 23-27 dyne range.
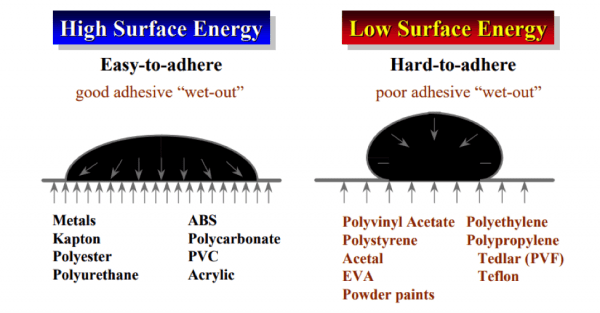
Adhesive Selection
Rubber based adhesive tapes will develop good adhesion to most surfaces down to about 30 dyne/cm. This wide adhesion range is great from an adhesion standpoint. However, if the application requires UV resistance, chemical resistance or high temperature resistance, many rubber-based systems will not perform well.
Acrylic adhesive tapes don’t have the same limitations with UV, chemical or temperature resistance that the rubber-based adhesives do. But these acrylic adhesive tapes do have a narrower adhesion range. Selecting the best candidates require a little more care. For ease of understanding, acrylics can be classified into three broad groups: pure acrylics, modified acrylics and LSE acrylics.
Pure acrylics (no modifiers) are good choices for bonding to metals, glass and other surfaces down to about the mid 40 dyne level. Modified acrylics have added tackifiers that extend the adhesion range down to the upper to mid 30 dyne level. LSE acrylics can even go a bit lower.
Surface Roughness
The unaided human eye can resolve objects down to roughly 100 microns (0.1mm). Surfaces that look and feel smooth can have very interesting surface features when viewed under magnification. For example, look at the stainless steel images below.
Surface textures such as embossing, stippling and coatings add aesthetic beauty and functionality such as anti-slip, stain resistance and a host of other benefits. The topography of these textures must be accounted for when selecting the best tapes.
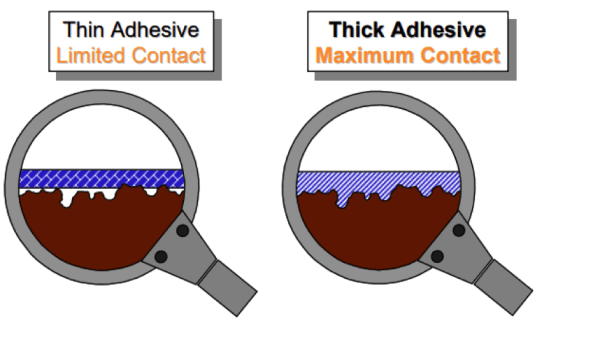
The pressure sensitive adhesives on tapes behave like both a solid and a liquid. This property is called viscoelastic behavior. The diagram above shows the benefit of selecting the appropriate adhesive thickness to maximize the “flow” of the adhesive into the valleys of the surface topography that will maximize bond strength.
For most industrial bonding applications, tape manufacturers typically offer tapes with adhesive thicknesses in the 1 mil (25 microns) to 5 mil (125 micron) range that will handle the majority of metal, glass and plastic bonding. Duct tapes and other specialty products contain even thicker adhesive coatings to handle porous surfaces such as concrete.
Summary
Tapes bond to surfaces without changing the inherent characteristics of that surface. The molecular force of attraction along with some mechanical interlocking determine ultimate adhesion. Also, the strength of that attraction serves as a function of understanding surface energy.
Often the first question asked by those in the tape business center around understanding the surface(s) involved in bonding. The surface chemical structure along with any information on coatings, treatments and texture provide additional insight into selecting the best tape for the application.
Have a question about tape bonding? Contact Tom Brown, Inc. today!