What Is Spooling?
Spooling is a process where rolls of tape products can be spliced together and wound onto a common core, similarly to fishing line or thread wound onto a reel. This traverse winding process allows significant footage to be wound onto a single roll without becoming excessively large and difficult to handle.How Spooling Benefits Your Process
Spooling allows your machines to keep running longer and thereby reducing costs associated with downtime, labor and changeovers.- More material per spool as compared to pancake rolls
- Fewer changeovers per shift
- More up-time on automated equipment
- Decreases downtime
- Saves warehouse space
- Quicker run-times
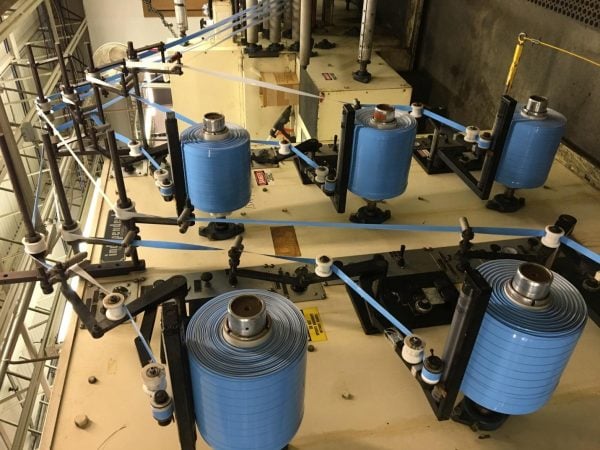
What Tape Products Can Be Spooled?
The more common types of tapes typically spooled are:
- Double coated foam tapes
- Single coated foam tapes
- Double Coated Film Tapes
- Nonwovens and tissue supported tapes
Specialized Spooling Services
There are some tapes that are difficult to spool, namely acrylic foam tapes (VHB type tapes) and unsupported transfer adhesives. These products are challenging because they tend to “knit” back together along the edges. Tom Brown has the right spooler to solve this issue and successfully spool these products. A slightly wider secondary liner can be introduced just prior to application and the tape will spool beautifully. There are some tape products that need a finger lift, or dry edge, along one side for the tape to facilitate easy release liner removal. Tom Brown has the right equipment to add a dry edge and wind a functional, attractive spool package.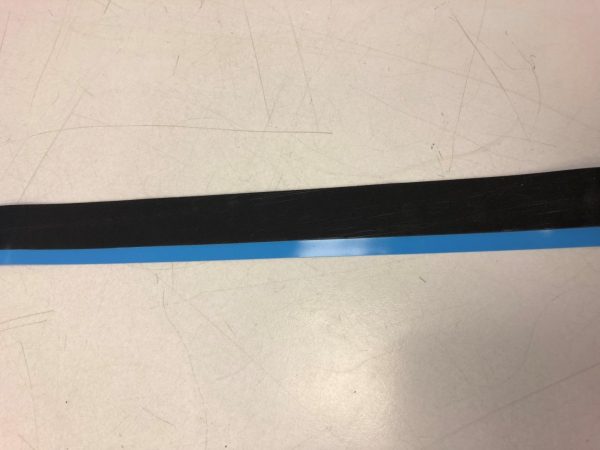
Critical Spooling Parameters
It’s important to discuss the “put up” or spool configuration with your supplier to make sure the spools work as intended.
The first thing you typically discuss is the required width of the tape and the requested length of the spool. This discussion usually goes hand-in-hand with the core diameter and spool width. The most common core diameters for spooling jobs are 3” or 6”. But spool widths can vary greatly, with 6”-12” wide spool packages as the most common.
The thickness of the tape, the spool width, and the machine’s capabilities are three factors that most influence how long the spool can be. The thinner the material, the more you can put on the spool. A 3” ID core can usually be wound with additional material (up to a point), but is a little harder to handle. With a 6” core, you sacrifice a little length, but the spool package is a little easier to maneuver.
For example, a 1/16” double coated foam tape can be spooled on a 7”-10” width spool with anywhere from 2,500- 4,700 ft depending on the three factors mentioned above.
By adjusting the “pitch” – the distance between the adjacent winds of tape and the “dwell” (how long the traversing head stays on the edge prior to making the next pass or layer) – you can create different types of spools:
- Normal
- Pineapple
- Pancake
- Fixed Lobing
- Cyclic
- Step Pack
Want to know more about spools and how they can help your process? Contact Tom Brown, Inc. today.