Many of you have probably used duct tape or masking tape during the winter months and might have noticed that it doesn’t seem quite as “sticky” as it normally does. This reduction in tack or “stickiness” is normal and will become more noticeable as the temperature drops below 40°F. Let’s explore why this happens.
Glass Transition Temperature
The glass transition temperature (abbreviated Tg) is a point at which a polymeric material like a pressure-sensitive adhesive changes from a flexible, rubbery state to a more glasslike solid surface. The Tg can be measured by a piece of analytical equipment called a DSC or ‘Differential Scanning Calorimeter”. The DSC generates a graph or plot which you can use to calculate the approximate Tg. It is important to understand that the Tg is not a sudden event; it happens over a range but you can easily see the zone where this transition starts to occur on the graph below.
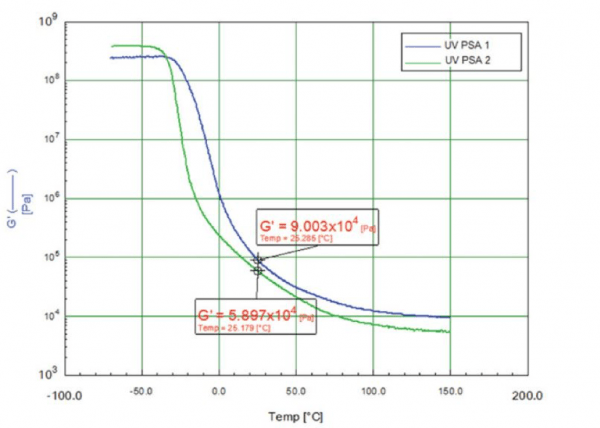
Why is This Temperature Important?
Tapes are used in a variety of applications such as bonding dissimilar surfaces, protection, bundling, etc… An engineer wants to be sure that tape that has been selected can operate within the temperature range his product will experience while accounting for the forces that will be present. A perfect example would be attaching an emblem or trim to a car. This application normally requires a double coated acrylic foam tape. The tape will see temperatures well below zero in Minnesota and well above 100°F in Arizona in the summer. On top of that it has to survive multiple trips through high pressure car washes, driving rain, dust, snow, and sleet and be able to dissipate shock when hitting potholes and being bumped. The engineer must account for all of that in his design and more. We as consumers just want the emblem to stay on our car. Period.
Application Temperature and Service Temperature
It is fairly common to see application temperature and service temperature listed on technical data sheets. It is important to understand the differences because both ranges contain important information.
The application temperature lists the range recommended by the manufacturer for applying the tape in the field or in a factory. It is not uncommon to see an application temperature range of 50-120˚F for many tape products. If you attempt to apply the tape below that recommended range, you will notice that the tack decreases and it is harder for the tape to “wet out” the surface and bond properly.
Having said that, tape manufacturers do offer tapes that can be successfully applied below 50˚F. There are applications particularly in the building and construction market where there is a need for tapes that can be applied at much lower temperatures. Adhesive chemists have been able to select specific raw materials such as rubbers and resins for rubber based systems or monomers for acrylic adhesives that have lower overall Tg values and offer better tack as the temperatures drop.
The service temperature range is much broader than the application range. This range assumes that you have established a bond within the recommended application range and allowed sufficient dwell time for the adhesive to completely wet out the surface (usually 24-72 hours). Once bonded, many adhesive systems can tolerate exposures to temperatures well below 0˚ and well above 150˚F in most cases. Silicone adhesives can tolerate temperatures down to -100F and up to +500F. Most acrylic adhesive tapes can tolerate -40F to+300F and even higher.
Learn More with Tom Brown, Inc.
Want to know more about low temperature performance? Contact Tom Brown, Inc. today